Laser-Cleaning verbessert die Batterieproduktion
Welche Ablenkeinheiten eignen sich für das Laser-Reinigen in den unterschiedlichen Anwendungsgebieten der Batterieherstellung?
Die Laserreinigung ist grundsätzlich ein sehr innovatives Verfahren, das völlig berührungslos zumeist mittels Faserlaser zur Entfernung von Rost, Oxiden, Farbe und anderen Beschichtungen von metallischen Oberflächen eingesetzt wird. Der große Vorteil: Es verändert die Eigenschaften des Materials dabei nicht. Laserreinigung benötigt keine Chemikalien oder Verbrauchsstoffe und ist daher deutlich umweltfreundlicher und ökologischer als herkömmliche Verfahren, die mit Säuren, Lösungsmitteln oder mechanischem Abrieb, wie z. B. Sandstrahlen, zum Reinigen arbeiten. Das Laser-Cleaning wird vermehrt auch zur Vorbehandlung für die Funktionalisierung von Oberflächen eingesetzt, um diese für die anschließenden Fertigungsschritte vorzubereiten. – So auch bei der Batterieproduktion, die angetreten ist, die Welt von fossilen Energieträgern unabhängiger zu machen.
Die Batterieindustrie profitiert enorm von modernen Lasertechnologieverfahren. Der Laser verringert bei der Produktion, z. B. von Lithium-Ionen-Batterien für Elektrofahrzeuge und Energiespeichersystemen, den Kostendruck und beschleunigt die Produktzyklen. Abgestimmte Lasersysteme, bestehend aus Laser und Laserablenkeinheit, erzielen unvergleichlich gute qualitative Ergebnisse – auch beim Cleaning. Noch auf winzigstem Raum arbeiten Lasersysteme hochdynamisch, vollautomatisiert wiederholbar und absolut präzise.

Laser-Cleaning von Oberflächen in der Batterieproduktion
Die Herstellung von Batterien erfordert zahlreiche geschweißte und geklebte Verbindungen, welche für die Funktionsfähigkeit des Produktes kritisch sind. Klebstoffe, Dichtstoffe, Pasten, Vergussmassen, Lückenfüllungen und Verkapselungen werden genutzt, um der Batterie thermische, strukturelle, abdichtende und dämpfende Eigenschaften zu verleihen. Das Entfernen von Verunreinigungen vor dem Kleben oder das Behandeln der Batterie verbessert die chemischen Eigenschaften, die die Teile zusammenhalten, und bestimmt die Leitfähigkeit der Kontakte und verbessert die Lebensdauer der Batterie. Bei den neuesten strukturellen Batterietechnologien kommt es besonders auf gute Oberflächenverbindungen an. Denn hier wirkt sich die Qualität der mechanischen Verbindung auf die Fahrzeugfestigkeit und damit auf die Gesamtsicherheit des Fahrzeugs aus.

Eine prismatische Zellhülle wird mit einem gepulsten Faserlaser lasergereinigt. Quelle Laserax
Laserreinigung vor dem Kleben und Schweißen
Eine gute Verschweißung und Verklebung beginnt immer mit der sorgfältigen Vorbereitung der Oberfläche – sprich mit ihrer Reinigung. Sie trägt zu einer besseren Haftfähigkeit der Klebstoffe bei. In Akkus gibt es auf Zellebene hunderte oder sogar tausende von Schweißnähten und geklebten Komponenten, die allesamt kritisch für das Funktionieren der Batterie sind. „Die Laserreinigung ist dabei ein hochpräziser, gleichmäßiger und schneller Prozess, der jegliche Art von Kontamination durch Elektrolyte, Staub, Öle und Oxide von Metalloberflächen entfernt. Die Batteriekomponenten bleiben vom Cleaning unberührt und intakt“, betont Alex Fraser, Laserax Vice President (VP) and Chief Technology Officer (CTO). Das kanadische Unternehmen mit Hauptsitz in Quebec und Tochter in Bad Grötzingen in Baden-Württemberg setzt im Cleaning-Prozess von Batteriekomponenten vermehrt auch auf RAYLASE Laserablenkeinheiten. Laserax Vice President (VP) and Chief Technology Officer (CTO) Alex Fraser: „Die Laserreinigung ist die beste Lösung zur Vorbereitung einer Batterieoberfläche. Sie wird von vielen wichtigen Klebstoffherstellern empfohlen. Reinigungszonen können extrem flexibel für unterschiedlichste Teilegrößen und -formen positioniert werden. Wir setzen seit 2013 auf Laserablenkeinheiten von RAYLASE, was uns eine sehr effiziente Reinigung bei hohen Produktionsraten ermöglicht.“
Perfekte Reinigung von elektrischen Kontakten
Die technischen Anforderungen an die Produktion von Batterien sind in jedem Produktionsschritt enorm. Batteriemodule haben Hunderte bis Tausende von Polen, die vor dem Schweißen gereinigt werden müssen, sodass selbst eine Abweichung von 1 % zu massiven Rückrufaktionen führen kann. Und die sind teuer und rufschädigend! In der Laserschweiß-Industrie reicht eine Präzision von 6 Sigma einfach nicht mehr aus, es benötigt 7 Sigma: 0,019 Fehler pro Million Schweißungen. Die Laserreinigung bietet hier die erforderliche Präzision, um konsistente Reinigungsergebnisse zu gewährleisten und Qualitätsprobleme zu vermeiden. „So werden die Kontakte, z. B. von Pouchzellen, berührungslos
in unübertroffener Geschwindigkeit gereinigt, sodass reine Stromverbindungen zwischen unterschiedlichen Metallen wie Kupfer und Aluminium ohne störende Einflüsse von Fremdpartikeln wie Lack, Epoxid oder Öl gewährleistet werden können“, erklärt Frédéric Faity, Technical Sales Manager bei RAYLASE, den komplexen Produktionsprozess. Mit seiner Präzision und Geschwindigkeit ist der vollautomatisierte, kontaktlose Laserabtragungsprozess von Verunreinigungen auf Batterie-Sammelschienen und Batterie-Submodulen einfach unübertroffen in seiner Qualität.
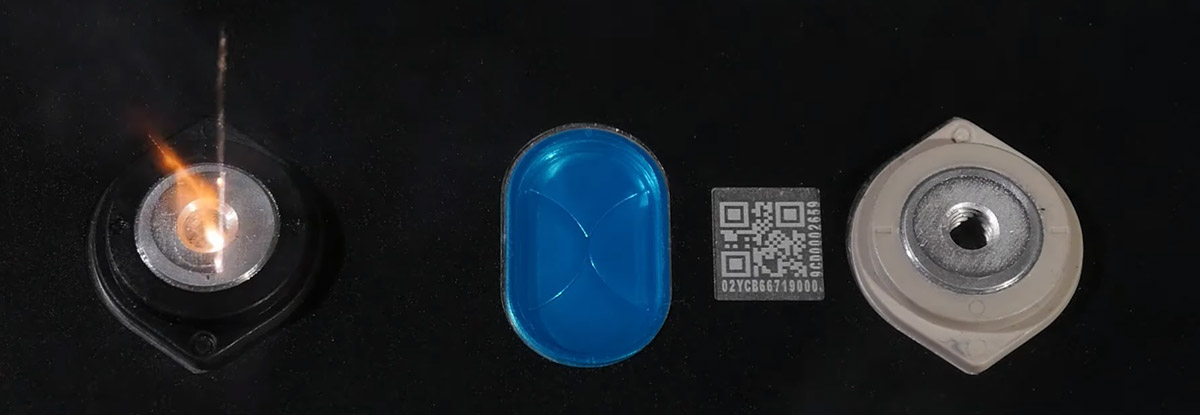
Quelle Laserax
Für das blitzschnelle, hocheffiziente Reinigen von Batteriekomponenten bietet RAYLASE als Einstiegsmodell die MINISCAN III Serie und als High-End-Produkt den SUPERSCAN IV-15 an. Das Arbeiten über mehrere Ebenen ermöglicht der FOCUSSHIFTER-14.
MINISCAN III SERIE
Kompakt, performant, kostensparend
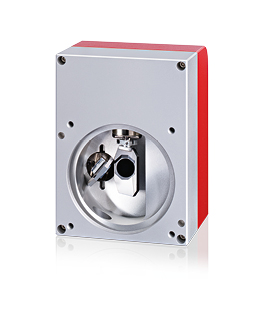
SUPERSCAN-IV-15
Hohe Geschwindigkeit & hohe Präzision
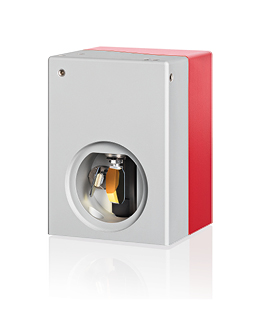
FOKUSSHIFTER-14
Reinigung von 3D-Oberflächen

Der Wasserkontaktwinkeltest zeigt den Reinigungserfolg
Vertrauen ist gut, Kontrolle ist besser! Zur Prüfung der Reinigungsresultate setzt Laserax einen Wasserkontaktwinkeltest ein. Der Winkelgrad visualisiert das Ergebnis der Laserreinigung: Bei einem flachen Winkel unter < 10° mit geringer Oberflächenspannung zeigt der Test, dass hier gut gereinigt wurde. Ein steiler Winkel (Tropfen rechts) mit ca. 75° hoher Oberflächenspannung lässt auf eine schlecht gereinigte Stelle schließen.

Oxidentfernung auf Batteriezellen
Wenn brennbare Stoffe mit Sauerstoff reagieren entstehen Oxide. Bei der Batterieherstellung sind das meist Metalloxide, die den Stromfluss behindern können. Sie müssen vor Schweiß- oder Verbindungsprozessen entfernt werden. Dabei ist die Laseroxidentfernung ein gutes Mittel der Wahl. Sie kann Oxide auf sehr sanfte Art entfernen, ohne das Grundmetall darunter zu verunreinigen. Mit der Mikrometerpräzision des Lasers lassen sich Oxide in kontrollierten Schichten und von vordefinierten Bereichen reinigen. „Mit unseren Lasersystemen können Oxide und andere Verunreinigungen schnell und vollständig entfernt werden, Besonderheiten: ohne dass das darunter liegende Metall beschädigt wird“, betont Stéphane Melançon, EV Expert at Laserax.

Die Oberseite einer zylindrischen Zelle, links vollständig mit Oxid kontaminiert und rechts nach der Laserreinigung. Quelle Laserax
Besonderheiten: RAYLASE bietet einzigartige, für diese Anwendungen ausgelegte opto-dynamische Möglichkeiten und mannigfache Auslegungsvarianten seiner Ablenkeinheiten.

RAYLASE Ablenkeinheit SUPERSCAN-IV
Vorteile:
- Enorme Produktivitätssteigerung bei gleichzeitig weniger Ausschuss
- Passende Auslegungsvarianten je nach Anforderung
- Höchste Laserpulsleistungen bis 2 kW möglich
Die vorfokusssierende RAYLASE Ablenkeinheit SUPERSCAN-IV eignet sich besonders für sehr schnelle und präzise Einsätze im Cleaning-Bereich. Quelle RAYLASE
Entfernung von Beschichtungen auf Zellfahnen
Die gebräuchlichsten Methoden zur Entfernung von Beschichtungen umfassen Abbrennöfen, Sandstrahlen und chemisches Abbeizen. Die Laserreinigung hat sich dort als besonders gut erwiesen, wo Geschwindigkeit und Präzision eine große Rolle spielen – wie eben in der Batterieproduktion.

Die Elektrodenfahnen einer Pouch-Zelle werden mittels Laser von Isolierbeschichtungen gereinigt und so auf den weiteren Schweißprozess mit dem Stromabnehmer vorbereitet. Quelle Laserax
Die Vorteile der Laserreinigung für Batteriezellen auf einen Blick:
- Enorme Produktivitätssteigerung
- Gleichbleibende Reinigungsqualität
- Schützt umliegende Bauteile vor Verbrennungen
- Hochpräzise Positionierungen auf kleinstem Raum
- Vermeidet teure Rückrufaktionen aufgrund mangelhafter Schweißnähte
- Deutlich weniger Ausschuss, mehr Nachhaltigkeit
- Umweltfreundliche und ökologische Prozesse – kein Abrieb, keine Chemikalien
RAYLASE bietet innovative Gesamtlösungen bestehend aus der Laserablenkeinheit, der Steuerkarte SP-ICE-III und der Software RAYGUIDE, maßgeschneidert für die jeweilige Laser-Cleaning-Aufgabe.
Das Unternehmen Laserax, Kanada

„Wir bei Laserax glauben an die Kraft der Lasertechnologie, um Fertigungsprozesse zu verbessern und sie effizienter und nachhaltiger zu gestalten. Diese Power wird die Welt weiter verändern“, davon ist Laserax Vice President (VP) and Chief Technology Officer (CTO) Alex Fraser überzeugt. 2010 gegründet, entwickelte das Unternehmen zunächst Inline- Laserlösungen für große Schmelzwerke. Seitdem erobert es von seinem Headquarter in Quebec, Kanada aus Gießereien und Automobilzulieferer auf der ganzen Welt.
Laserax bringt hochinnovative Lasertechnologien auf den Markt. Die Kanadier bieten u. a. manuelle und automatisierte Laserreinigungsmaschinen an, die Farbe, Oxide, Rost und andere Verunreinigungen von Metalloberflächen schnell und hochpräzise entfernen. Zudem wird die Oberflächenhaftung durch Lasertexturierungen verbessert. Laserax entwickelt dabei sowohl komplette Laserlösungen als auch Hochleistungslaser, die Oberflächen markieren, reinigen, strukturieren und härten.
Gemeinsam die Zukunft der industriellen Produktion zum Positiven verändern: „In der Verbindung unserer Stärken liegt viel Potenzial“, davon ist RAYLASE CEO Dr. Philipp Schön überzeugt.
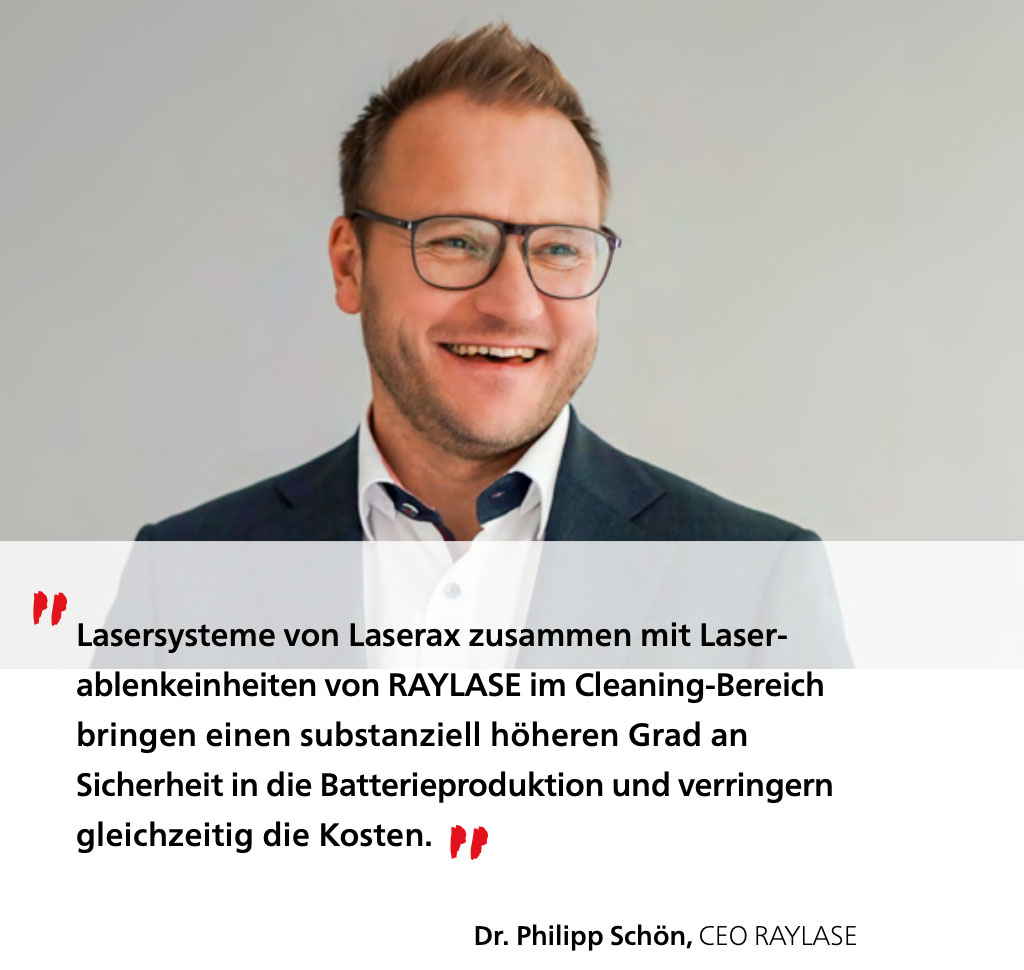