FIELD CALIBRATION FOR AM-MULTI-HEAD MACHINES
Productivity increase beyond an optimized exposure process
QUICK FINDER
- AT A GLANCE
- PERIODIC SCAN FIELD CALIBRATION ENSURES RELIABLE ADDITIVE PRODUCTION
Manual calibration is time – consuming and inaccurate
Coordinate measuring machine – precise, expensive and slow?
The challenge multi-head-system - FAST MEASUREMENT AND CONVENIENT CORRECTION WITH THE SFC
All-in-one solution for scan field calibration
Optimized functionalities for AM multi-head systems - BOOSTING EFFICIENCY IN ADDITIVE MANUFACTURING
AT A GLANCE - HIGHER PRODUCTIVITY WITH AN OPTIMIZED CALIBRATION SOLUTION

- High complexity with multi-laser AM machines: The production with AM multi-head systems is significantly more demanding than with a single AM machine. This is because optimum results can only be ensured long-term if all components and processes interact efficiently. Still, the productivity gain is often decisive for the success of an AM application.
- Inaccurate calibration as a possible cause of component deviations: Sub-optimal integration of the deflection units or inadequate calibration can lead to deviations in the parts produced. These inaccuracies can impair product quality and lead to increased reject rates. This in turn drives up production costs.
- Adapted calibration processes for multi-field systems: Through the use of advanced technologies and specialized processes, such as the SCAN-FIELD-CALIBRATOR, precise and repeatable calibration of all working fields is achieved. This minimizes the risk of errors and ensures consistent results across all production runs.
- Increased productivity through optimized accompanying processes: With improved calibration and integration processes, companies can reduce their lead times and minimize reject rates. This not only leads to cost savings, but also increases the profitability and efficiency of the entire manufacturing process.
PERIODIC SCAN FIELD CALIBRATION ENSURES RELIABLE ADDITIVE PRODUCTION
Do you know this? Your delivery is delayed because the FAT calibration takes days. Or do you have a bad feeling about the current production run because you have again postponed recalibration for time reasons so as not to delay production?
In additive manufacturing, scan field calibration is of significant importance for the quality of the manufactured components. This is because a precise correction file ensures that the laser beam hits where it should - in the entire scan field.
If this is not the case, inaccuracies or deviations can lead to component errors, reduced strength, or even component failure. For machine operators, these errors could result in high costs for rejects, rework, or warranty claims. Especially if you operate in a series production environment where consistency and repeatability are crucial. Therefore, accurate initial calibration and regular calibration checks are crucial for reliable production.
manual calibration is time – consuming and inaccurate
But without the right tools, even calibrating a single scan system can be a laborious task. If you measure the individual points manually, it is difficult to achieve sufficient accuracy and reproducibility. Measuring errors due to incorrect positioning of the measuring ruler or parallax errors when reading the measured value occur regularly because recording a large number of measuring points can be quite tiring.
Since a very accurate reading is crucial, precise measurement takes a lot of time. With a high resolution of 49 x 49 measuring points, this can quickly add up to several working days of measuring time. For this reason, manual calibration usually involves working with significantly fewer measuring points, for example, 11 x 11 measuring points. This results in significantly less homogeneity across the scan field and correction accuracies of +/- 50 µm. But this precision is not sufficient for many processes in additive manufacturing or electromobility.

Figure 1: Manual measurement of calibration plates. For the manual calibration of an AM machine, markings are inscribed on a plate in the scan field and then measured. The read values are then transferred to the editor and the deviations are determined and corrected.
With manual calibration, the measurement takes a long time and errors such as transposed numbers can easily occur during transfer. For this reason, this method only achieves average accuracies of +/- 50 µm.
Coordinate measuring machine: Precise, expensive and slow?
When companies require greater accuracy in their AM machines, many think about investing in a coordinate measuring machine - even if such measuring machines with good accuracy often cost more than EUR 150,000 to purchase. After all, a coordinate measuring machine can save a lot of time by not only measuring a panel accurately but also automatically. With regular calibrations, such a purchase can therefore be well worthwhile.
Nevertheless, it still takes time for the results to be available. The measurement is carried out serially and point after point must be approached and precisely measured. A few seconds quickly pass per data point, so several hours still pass for a precise calibration with 49 x 49 measuring points (e.g. 5s x 49 x 49 = 12000s = 3.33h). This particularly becomes a problem when many machines are to be calibrated.
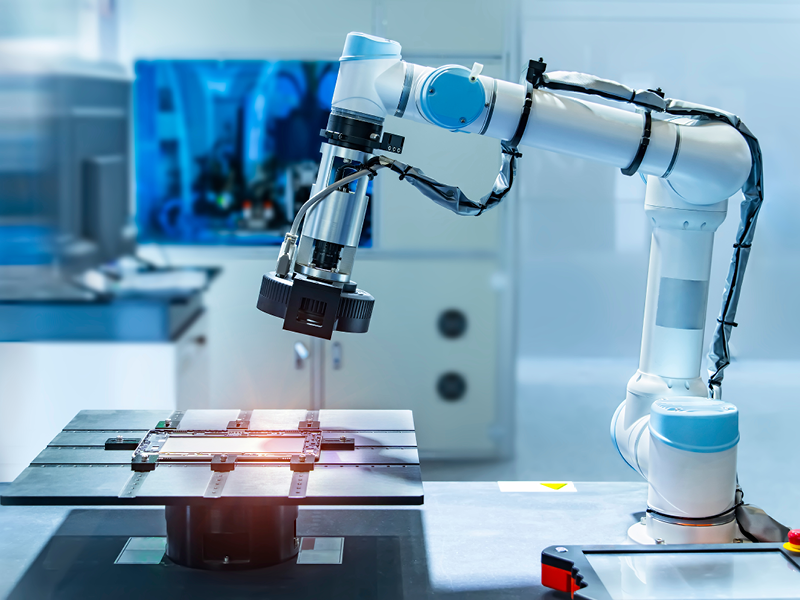

The challenge of a multi-head system
This challenge is particularly evident when calibrating multi-head systems, as the number of calibration plates multiplies with the number of heads. For a multi-laser system with four deflection units, we now need four measurements for the calibration process.
Assuming that for the initial calibration of an AM machine, the scan field is measured twice, once for the correction and then again for checking, the initial calibration of a four-head system in production takes over 3 working days of pure measuring time (2x 4x 3.33h = 26.66h). On top of this, there are often another 3 working days for the measurements as part of a FAT and a SAT.
Regular calibration is also necessary and important when operating an AM multi-head machine. If you only want to recalibrate your machine once a month, one coordinate measuring machine can operate around 12 AM four-head systems. This may sound like a lot to some AM job shoppers, but in industrial additive production, calibration can quickly become a bottleneck.

Figure 2: Deflection units with overlapping scan fields for an AM multi-head system. For maximum productivity or large scan fields, several deflection units are grouped together to form a multi-head system. The overlapping scan fields not only need to be calibrated within themselves but also aligned with each other. Only in this way can the full performance of all lasers be utilized.
FAST MEASUREMENT AND CONVENIENT CORRECTION WITH THE SFC
With the SCAN-FIELD-CALIBRATOR, the required time for a single calibration can be reduced to just a few minutes. Instead of approaching each measuring point in series, the SFC scans the calibration plate with a highly accurate, telecentric and calibrated flatbed scanner. This allows you to achieve absolute accuracies of approx. +/- 15 μm, mostly significantly lower which is comparable to the accuracy of a coordinate measuring machine. Still, it requires much less time for this task.
In addition, the SFC places markers on the calibration plate during marking. This ensures correct orientation at all times. On top of this, also the z-position of the focus can be corrected with the SFC.
All-in-one solution for scan field calibration
The significantly shorter measuring time per calibration plate is of course a decisive advantage when calibrating multi-head systems. However, in addition, the SFC also offers another decisive advantage over a coordinate measuring machine: it is a one-stop solution adapted to the AM market. While a coordinate measuring machine is designed to cover a wide range of measuring tasks, the SFC has been developed specifically for the scan field correction of deflection units. This means that it covers and controls the entire calibration process. From controlling the deflection unit to set a suitable marking pattern, to measuring and evaluating the calibration plate, to creating and distributing the correction files via a shared network.
This has many advantages
- Additional markers are automatically included on the plate to ensure the correct orientation of the measurement
- The name of the user, the time, the calibration file and the temperature values are included in a QR code. This information can later be used for statistics, for example, to trace back certain phenomena in the calibration to e.g. environmental conditions
- Additional markers are marked and evaluated to determine the z-focus
- The measuring points can be clearly assigned to individual deflection units
- Data does not have to be transferred between different systems such as AM machine, measuring machine and evaluation software
- The calibration history is saved and can be easily reloaded and analyzed

Figure 3: Scan field calibration in XY. A) For calibration, a cross pattern is marked on a calibration plate in the scan field and then measured. From this measurement, a correction file is created for the deflection unit. B) Without a correction file, there is a significant deviation in the scan positions at the edges of the scan field. C) The calibration enables homogeneous control with only minimal deviations.

Figure 4: Calibration of an AM machine in z-direction. A) A line pattern with different focal lengths allows to determine the optimum focal plane. B) Without z-calibration, mechanical tolerances in the machine can lead to a tilted working plane. C) By using an additional z factor in the correction file, the tilting of the working plane can be compensated.
Optimized functionalities for AM multi-head systems
As a high-precision laser application, additive manufacturing has a particular need for frequent scan field calibration. Various AM requirements have therefore found their way into the SFC. In this context, the biggest challenge is the calibration of multi-head systems. Not only do the scan fields of the individual deflection units need to be precisely calibrated, but the scan fields also need to be optimally aligned with each other.
The multi-field option of the SFC helps with this task. The machine design is stored in advance in the SFC‘s control software, the SCAN FIELD MANAGER (SFM): the number of deflection units, the distances between the deflection units and the individual scan field sizes. The SFM then determines the optimum number and spacing of the calibration points and the required number of calibration plates. It also guides you through the calibration process, ensuring that it is carried out reliably and quickly.

Figure 5: Software interface for calibrating a joint overlapping working area. Using the multi-field option of the SCAN FIELD MANAGER (SFM), it is possible to map the arrangement of the deflection units including image fields and offsets. In addition, the scan field that needs to be calibrated is defined. With this information, the SFM calculates the optimum distribution of the markings and the required number of calibration plates. It then guides the user through the calibration process, ensuring optimum and correct calibration.
In multi-head systems with a common scan field of up to 600 x 600 mm², it is possible to measure several deflection units on a common plate instead of several individual plates. This allows you to carry out routine recalibrations between two build jobs in less time and the machine is ready for production again more quickly. In this calibration method, the measuring points of all deflection units are distributed in the scan field, not just at the edge. As the measuring points of several deflection units are distributed in the scan field, only a lower absolute accuracy is possible. However, the accuracy is typically sufficient to check the machine status and requires significantly less time to do so.
As a result, your AM machine always starts the construction process optimally calibrated. At the same time, the regular measurements enable detailed documentation of the machine status, as required for some applications in medical technology or the aerospace industry.

BOOSTING EFFICIENCY IN ADDITIVE MANUFACTURINg

In modern additive manufacturing, industrial companies are constantly focusing on increasing productivity. However, it is usually not enough to concentrate on the exposure process alone. The adjacent processes, such as powder management, data processing or scan field calibration, also offer a number of additional opportunities.
If you regularly calibrate AM systems and are considering investing in a coordinate measuring machine, then you should definitely take a look at the SFC as an application-specific complete solution for your calibration process. Because only by taking a holistic view and optimizing all processes can the full potential of your machine be exploited and maximum productivity and quality achieved.