Multifeld-Kalibrierung für AM-Mehrkopfsysteme
Produktivitätssteigerung jenseits eines optimierten Belichtungsprozesses
QUICK FINDER
- AUF EINEN BLICK
- REGELMÄSSIGE SCANFELDKALIBRIERUNG STELLT ZUVERLÄSSIGE ADDITIVE PRODUKTION SICHER
Manuelle Kalibrierung – Zeitaufwendig und ungenau
Koordinatenmessmaschine – Präzise, teuer und langsam?
Herausforderung Mehrkopfsystem - SCHNELLE VERMESSUNG UND BEQUEME KORREKTUR MIT DEM SFC
Komplettlösung für die Scanfeldkalibrierung
Optimierte Funktionen für AM-Mehrkopfanlagen - EFFIZIENZSTEIGERUNG IN DER ADDITIVEN FERTIGUNG
AUF EINEN BLICK – Höhere Produktivität durch optimierte Kalibrierlösung

- Hohe Komplexität bei Multi-Laser-AM-Maschinen: Die Produktion mit AM-Mehrkopfsystemen ist deutlich anspruchsvoller als die Verwendung einer einzelnen AM-Maschine. Denn nur bei einem effizienten Zusammenspiel aller Komponenten und Prozesse können optimale Ergebnisse dauerhaft sichergestellt werden. Dennoch ist der Produktivitätsgewinn mehrerer Laser häufig entscheidend für den Erfolg einer AM-Anwendung.
- Ungenaue Kalibrierung als mögliche Ursache für Bauteilabweichungen: Bei sub-optimaler Integration der Ablenkeinheiten oder mangelhafter Kalibrierung kann es zu Abweichungen in den produzierten Teilen kommen. Diese Ungenauigkeiten können die Produktqualität beeinträchtigen und zu erhöhten Ausschussraten führen. Das wiederum treibt die Produktionskosten in die Höhe.
- Angepasste Kalibrierungsprozesse für Multifeld-Systeme: Durch den Einsatz von fortschrittlichen Technologien und spezialisierten Verfahren, wie dem SCAN-FIELD-CALIBRATOR wird eine präzise und wiederholbare Kalibrierung aller Arbeitsfelder erzielt. Dies minimiert das Risiko von Fehlern und sorgt für konsistente Ergebnisse über alle Produktionsläufe hinweg.
- Produktivitätssteigerung durch optimierte begleitende Prozesse: Mit verbesserten Kalibrierungs- und Integrationsprozessen können Unternehmen ihre Durchlaufzeiten reduzieren und Ausschussraten minimieren. Dies führt nicht nur zu Kosteneinsparungen, sondern steigert auch die Rentabilität und Effizienz des gesamten Fertigungsprozesses.
Regelmäßige Scanfeldkalibrierung stellt zuverlässige additive Produktion sicher
Kennen Sie das? Die Auslieferung verzögert sich, weil sich die Kalibrierung im Rahmen der FAT über Tage zieht? Oder Sie haben ein ungutes Gefühl beim aktuellen Produktionslauf, weil Sie die Re-Kalibrierung aus Zeitgründen schon wieder aufgeschoben haben, um nicht die Produktion zu verzögern?
In der Additiven Fertigung ist die Scanfeldkalibrierung von entscheidender Bedeutung für die Qualität der hergestellten Bauteile. Denn eine präzise Korrekturdatei gewährleistet, dass der Laserstrahl dort trifft, wo er soll – und zwar im gesamten Scanfeld.
Ist das nicht der Fall, können Ungenauigkeiten oder Abweichungen zu Bauteilfehlern, einer verminderten Festigkeit oder sogar zum Versagen des Bauteils führen. Für Maschinenbetreiber könnten diese Fehler hohe Kosten für Ausschuss, Nacharbeit oder Garantieansprüche verursachen. Insbesondere wenn Sie in einem Serienproduktionsumfeld agieren, wo Konsistenz und Wiederholbarkeit von entscheidender Bedeutung sind. Deshalb sind eine präzise Erstkalibrierung und eine regelmäßige Überprüfung der Kalibration entscheidend für eine zuverlässige Produktion.
Manuelle Kalibrierung ist zeitaufwendig und ungenau
Doch ohne die richtigen Tools kann schon die Kalibrierung eines einzelnen Scan-Systems eine aufwendige Angelegenheit sein. Wenn Sie die einzelnen Punkte manuell vermessen, ist es schwierig eine ausreichende Genauigkeit und Reproduzierbarkeit zu erreichen. Messfehler durch falsches Anlegen des Messlineales oder Paralaxenfehler beim Ablesen des Messwertes kommen regelmäßig vor, weil das Erfassen sehr vieler Messpunkte durchaus ermüdend sein kann.
Da ein sehr genaues Ablesen entscheidend ist, kostet ein präzises Vermessen viel Zeit. Bei einer hohen Auflösung von 49 x 49 Messpunkten kommen hier schnell mehrere Arbeitstage an Messzeit zusammen. Daher wird bei einer manuellen Kalibrierung meist mit deutlich weniger Messpunkten gearbeitet, beispielsweise mit 11 x 11 Messpunkten. Doch das führt zu einer deutlich geringeren Homogenität über das Scanfeld und Korrekturgenauigkeiten von +/- 50 µm. Für viele Prozesse in der additiven Fertigung oder auch in der Elektromobilität reicht diese Genauigkeit aber nicht aus.

Abbildung 1: Manuelle Vermessung von Kalibrierplatten. Für die manuelle Kalibrierung einer AM-Maschine werden Markierungen im Scanfeld auf eine Platte beschriftet und anschließend vermessen. Die abgelesenen Werte werden dann in den Editor übernommen und daraus die Abweichungen bestimmt und korrigiert.
Bei einer manuellen Kalibrierung benötigt die Vermessung viel Zeit und beim Übertragen können leicht Fehler wie z. B. Zahlendreher passieren. Daher werden bei dieser Methode nur mittlere Genauigkeiten von +/- 50 μm erreicht.
Koordinatenmessmaschine: Präzise, teuer und langsam?
Wenn Unternehmen eine höhere Genauigkeit in ihrer AM-Maschinen benötigen, dann denken viele über die Investition in eine Koordinatenmessmaschine nach - auch wenn solche Messgeräte bei guter Genauigkeit in den Anschaffungskosten oft über 150.000 EUR liegen. Denn eine Koordinatenmessmaschine führt die Vermessung einer Platte nicht nur genau, sondern auch automatisiert durch und spart damit viel Arbeitszeit. Bei regelmäßigen Kalibrierungen kann sich eine solche Anschaffung also durchaus lohnen.
Trotzdem dauerte es auch hier, bis das Ergebnis vorliegt. Die Messung erfolgt seriell und Messpunkt für Messpunkt muss angefahren und präzise vermessen werden. Pro Datenpunkt vergehen schnell einige Sekunden, so dass für eine präzise Kalibrierung mit 49 x 49 Messpunkten weiterhin mehrere Stunden vergehen (z.B. 5s x 49 x 49 = 12000s = 3,33h). Das wird insbesondere dann zum Problem, wenn viele Maschinen kalibriert werden sollen.
Koordinatenmessmaschine: Präzise, teuer und langsam?
Wenn Unternehmen eine höhere Genauigkeit in ihrer AM-Maschinen benötigen, dann denken viele über die Investition in eine Koordinatenmessmaschine nach - auch wenn solche Messgeräte bei guter Genauigkeit in den Anschaffungskosten oft über 150.000 EUR liegen. Denn eine Koordinatenmessmaschine führt die Vermessung einer Platte nicht nur genau, sondern auch automatisiert durch und spart damit viel Arbeitszeit. Bei regelmäßigen Kalibrierungen kann sich eine solche Anschaffung also durchaus lohnen.
Trotzdem dauerte es auch hier, bis das Ergebnis vorliegt. Die Messung erfolgt seriell und Messpunkt für Messpunkt muss angefahren und präzise vermessen werden. Pro Datenpunkt vergehen schnell einige Sekunden, so dass für eine präzise Kalibrierung mit 49 x 49 Messpunkten weiterhin mehrere Stunden vergehen (z.B. 5s x 49 x 49 = 12000s = 3,33h). Das wird insbesondere dann zum Problem, wenn viele Maschinen kalibriert werden sollen.
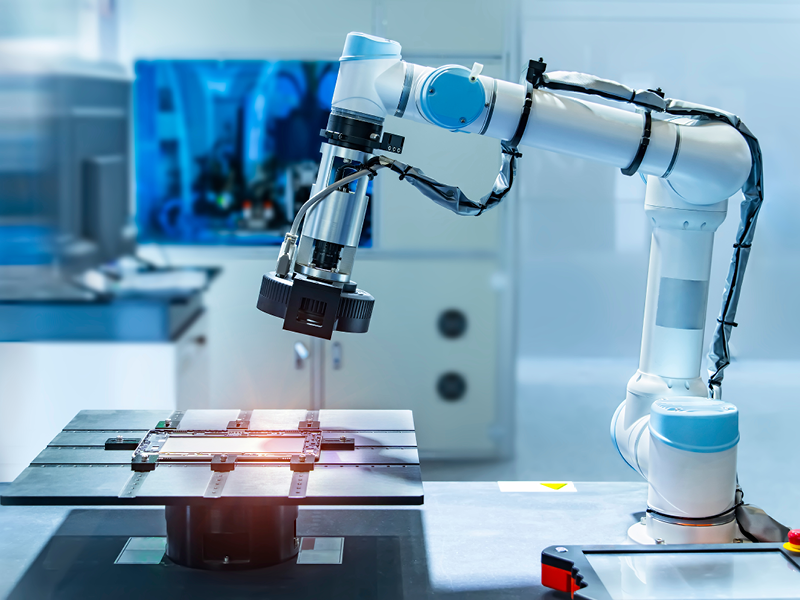
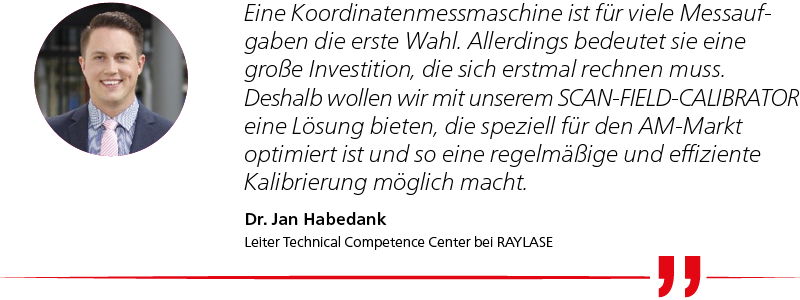
Herausforderung Mehrkopfsystem
Besonders deutlich wird diese Herausforderung bei der Kalibrierung von Mehrkopfanlagen. Denn hier vervielfacht sich die Anzahl der Kalibrationsplatten mit der Anzahl der Köpfe. Für eine Multilaser-Anlage mit vier Ablenkeinheiten werden nun gleich vier Messungen benötigt.
Wenn man davon ausgeht, dass für die initiale Kalibrierung einer AM-Maschine das Scanfeld einmal vermessen und nach der Korrektur noch einmal überprüft wird, dann dauert eine Erst-Kalibrierung einer Vierkopfanlage im Rahmen der Produktion über 3 Arbeitstage reine Messzeit (2x 4x 3,33h= 26,66h). Dazu kommen häufig noch weitere 3 Arbeitstage für die Messungen im Rahmen einer FAT und einer SAT.

Abbildung 2: Ablenkeinheiten mit überlappenden Scanfeldern für eine AM-Mehrkopfanlage. Für höchste Produktivität oder große Scanfelder werden mehrere Ablenkeinheiten zu einer Mehrkopfanlage gruppiert. Die überlappenden Scanfelder müssen dabei nicht nur in sich kalibriert werden, sondern auch zueinander ausgerichtet werden. Nur so kann die volle Leistungsfähigkeit aller Laser genutzt werden.
Schnelle Vermessung und bequeme Korrektur mit dem SFC
Mit dem SCAN-FIELD-CALIBRATOR kann der Zeitbedarf für eine Kalibration auf wenige Minuten reduziert werden. Statt die einzelnen Messstellen seriell anzufahren, scannt der SFC mit einem hochgenauen, telezenztrischen und kalibrierten Flachbettscanner die Kalibrierplatte. So erreichen Sie absolute Genauigkeiten von ca. +/-15 μm, überwiegend deutlich darunter und sind vergleichbar genau wie mit einer Koordinatenmessmaschine.
Zusätzlich werden durch den SFC bei der Markierung auf der Kalibrierplatte Marker gesetzt. So ist immer die korrekte Orientierung sichergestellt. Außerdem kann in Kombination mit dem SFC auch eine Korrektur der Fokusposition in z-Richtung vorgenommen werden.
Komplettlösung für die Scanfeldkalibrierung
Auch bei der Kalibrierung von Mehrkopfanlagen hilft die deutlich kürzere Messzeit pro Kalibrierplatte natürlich ganz entscheidend. Doch neben einer kürzeren Messdauer bietet der SFC auch einen weiteren entscheidenden Vorteil gegenüber einer Koordinatenmessmaschine: Er ist eine auf den AM-Markt angepasste Lösung aus einer Hand. Während eine Koordinatenmessmaschine eine Vielzahl von Messaufgaben abdecken soll, ist der SFC eigens für die Scanfeldkorrektur von Ablenkeinheiten entwickelt worden. Das bedeutet, dass er den gesamten Kalibrierprozess abdeckt und steuert. Von der Ansteuerung der Ablenkeinheit zum Setzen eines geeigneten Markiermusters, über das Vermessen und Auswerten der Kalibrierplatte, bis hin zum Erstellen und Verteilen der Korrekturdateien über ein gemeinsames Netzwerk.
- Es werden automatisch zusätzliche Marker auf die Platte mitmarkiert, die die korrekte Orientierung der Messung sicherstellen.
- In einem QR Code werden der Name des Users, die Zeit, die Kalibrierdatei und die Temperaturwerte mit aufgenommen. Diese Information kann später z.B. für Statistiken verwendet werden, um bestimmte Erscheinungen in der Kalibrierung auf z. B. Umgebungsbedingungen rückführen zu können.
- Es werden zusätzliche Marker zur Bestimmung des z-Fokus markiert und ausgewertet.
- Die Messpunkte können eindeutig einzelnen Ablenkeinheiten zugeordnet werden.
- Daten müssen nicht zwischen unterschiedlichen Systemen wie AM-Maschine, Messmaschine und Auswertesoftware transferiert werden.
- Die Historie der Kalibrierungen wird gespeichert und kann einfach wieder geladen und analysiert werden.
Das bringt viele Vorteile mit sich:

Abbildung 3: Scanfeldkalibrierung in XY. A) Für die Kalibrierung wird ein Kreuzmuster auf eine Kalibrierplatte im Scanfeld markiert. Diese werden anschließend vermessen. Aus der Positionsabweichungen wird ein Korrekturfile für die Ansteuerung der Ablenkeinheit erstellt. B) Ohne Korrekturdatei kommt es an den Rändern des Scanfeldes zu einer signifikanten Abweichung in der Scan-Positionen. C) Die Kalibrierung ermöglicht eine homogene Ansteuerung mit nur minimalen Abweichungen.

Abbildung 4: Kalibrierung einer AM Maschine in z-Richtung. A) Ein Strichmuster mit unterschiedlichen Fokuslängen ermöglicht es die optimale Fokusebene zu ermitteln. B) Ohne z-Kalibrierung können mechanische Toleranzen in der Maschine zu einer verkippten Arbeitsebene führen. C) Durch eine zusätzliche z-Anteil in der Korrekturdatei kann die Verkippung der Arbeitsebene ausgeglichen werden.
Optimierte Funktionen für AM-Mehrkopfanlagen
Die additive Fertigung als hochpräzise Laseranwendung hat besonderen Bedarf an einer regelmäßigen Scanfeldkalibrierung. Daher haben verschiedene AM-Anforderungen den Weg in den SFC gefunden. Dabei ist die größte Herausforderung die Kalibrierung von Mehrkopfanlagen. Denn dort sind nicht nur die Scanfelder der einzelnen Ablenkeinheiten präzise zu kalibrieren, sondern auch die Scanfelder untereinander optimal auszurichten.
Bei dieser Aufgabe unterstützt die Multifeld-Option des SFC. In der Kontrollsoftware des SFC, dem Scanfield Manager (SFM), wird vorab das Maschinendesign hinterlegt: die Anzahl der Ablenkeinheiten, die Abstände der Ablenkeinheiten zueinander und die einzelnen Scanfeldgrößen. Anschließend ermittelt der SFM die optimale Anzahl und Abstände der Kalibrierpunkte sowie die nötige Menge an Kalibrierplatten Außerdem führt er durch den Kalibrierprozess und stellt so eine zuverlässige und zeitsparende Durchführung sicher.

Abbildung 5: Softwareoberfläche zur Kalibrierung eines gemeinsamen überlappenden Arbeitsbereichs. In der Multi-Feld-Option des SCAN FIELD MANAGER (SFM) wird die Anordnung der Ablenkeinheiten samt Bildfeldern und Offsets abgebildet. Außerdem wird das zu kalibrierende Scanfeld festgelegt. Mit diesen Informationen berechnet der SFM die optimale Verteilung der Markierungen und die nötige Anzahl an Kalibrierplatten. Anschließend führt er durch den Kalibrierprozess und stellt so eine optimale und korrekte Kalibrierung sicher.
Bei Mehrkopfanlage mit einem gemeinsamen Scanfeld von bis zu 600 x 600 mm2 ist es möglich, mehrere Ablenkeinheiten auf einer gemeinsamen, statt mehreren einzelnen Platten zu vermessen. So können Sie regelmäßige Re-Kalibrierungen zwischen zwei Baujobs in kürzerer Zeit durchführen und die Maschine ist schneller wieder produktionsbereit.
Bei dieser Kalibrationsmethode werden die Messpunkte aller Ablenkeinheiten im Scanfeld verteilt, nicht nur am Rand. Da die Messpunkte von mehreren Ablenkeinheit im Scanfeld verteilt werden ist damit nur eine geringere absolute Genauigkeit möglich. Allerdings reicht die Genauigkeit typischerweise aus, um den Maschinenstatus zu prüfen und benötigt dafür deutlich weniger Zeit.
So wird sichergestellt, dass Ihre AM-Maschine immer optimal kalibriert in den Bauprozess startet. Gleichzeitig ermöglichen die regelmäßigen Messungen eine detaillierte Dokumentation des Maschinenstatus, wie er bei manchen Anwendungen in der Medizintechnik oder der Luft- und Raumfahrt gefordert wird.
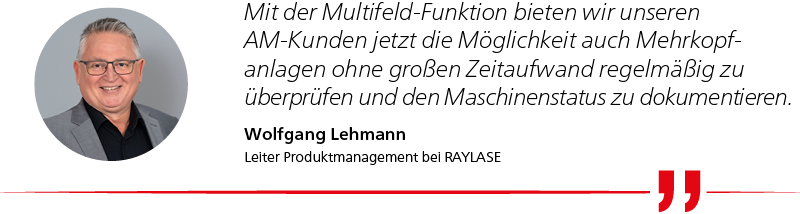
EFFIZIENZSTEIGERUNG IN DER ADDITIVEN FERTIGUNG

In der modernen Additiven Fertigung ist die Steigerung der Produktivität ständig im Fokus von Industrieunternehmen. Doch dabei reicht es meist nicht aus, wenn Sie sich ausschließlich auf den Belichtungsprozess konzentrieren.
Auch die umgebenden Prozesse, wie das Pulvermanagement, die Datenverarbeitung oder eben die Scanfeldkalibrierung bieten einige Ansatzpunkte.
Wenn Sie regelmäßig AM-Anlagen kalibrieren und mit dem Gedanken spielen, in eine Koordinatenmessmaschine zu investieren, dann sollten Sie unbedingt einen Blick auf den SFC als anwendungsspezifische Komplettlösung für Ihren Kalibrierprozess werfen. Denn nur durch eine ganzheitliche Betrachtung und Optimierung aller Prozesse kann die volle Leistungsfähigkeit Ihrer Maschine ausgeschöpft und ein Höchstmaß an Produktivität und Qualität erzielt werden.